I have no idea (no intention to know) the existence of control surface servo calculation , until I crash my F16 and blue angle. The 2 crashes resulted from inability to pull back the plane from a very high speed dive >150kph. It seems the plane cannot escape from the vertical dive.
Then I realise the importance of calculating the control surface servo torque requirement. To my surprise, the torque requirement is not linear.
For example , the elevator flap of my F16 measured as a triangular surfaces with chord 7cm and length 12cm, deflection 30deg, servo travel 45degree .
At speed of 100kph, the 2 flaps exert a torque of 8Ncm. (http://www.csd.net/~cgadd/eflight/calcs_servo.htm) My Towerpro 9G servo of 11Ncm is enough.
But at a speed of 150kph, the requirement is 18Ncm, which exceed the servo spec.
That result in crash....from a high dive at full speed.
Saturday, December 29, 2007
Wednesday, December 19, 2007
OS50 suddenly lost power - fixed
Suddenly lost power after 50 flights. The OS50 shows signs of overheat after 2-3 tic toc and the Carbsmart tends to richen the needle. Head temperature reads ~130 degC. Normally it reads <110deg C as adjusted in the carbsmart.
Turn out to be the damaged ring and sleeve (previous scotched) .
After replacing them, it works pretty well again.
Turn out to be the damaged ring and sleeve (previous scotched) .
After replacing them, it works pretty well again.
Sunday, December 16, 2007
F18 Blue Angle reach 120km/h airspeed!
.jpg)
My Align Team.
.jpg)
Align F16 400, modified with twin vertical fin.
Wt . of plane 350g + 210g (3s lipo)
450T/1800kv/2200mAh 18c/35A ESC
It reaches top speed of 107km/h at 280W with 3s.
.jpg)
Then, 4s 18c lipo of wt. : 280g
At 4s it pulls 380W, reaches my record breaking of 124 km/h.
With 6x5.8, motor is slight warm. Unlimited vertical.
With 7x7 propeller, the speed is not impressive and the motor is hot.
Another test flight with 3s/3000kv 450TH/5x5 APC, pulls >38A and speed ~ 110km/h. Acceleration is not impressive. Cannot performed vertical> 4s.
3s/3000kv/4.75x 4.75, pulls 32A, though calculated pitch speed>150km/h, but the thrust cannot overcome the drag to produce enough acceleration to reach the desired pitch speed. Unfortunately, I found my propeller mount slipping against the shaft and may result in the poor performance.
Tuesday, December 11, 2007
Align Muffler Pressure Hose
The engine sudden lost power on tic-toc and was richen with lots of smoke. The CSM carbsmart is working and richen the fuel to prevent engine overheating. On landing and found the pressure hose copper adapter has stripped the thread in the muffler.
I replaced the original 4mm copper adapter to a 5mm one (cost only HKD 10).
Saturday, December 08, 2007
New Z50 780kv motor
Wednesday, December 05, 2007
CSM Carb Smart temperature sensor
Installation pretty easy.
I take away the power source "signal wire" as early user complain the feedback "signal wire" may jam the (JR) receiver.
Remove the needle valve retch.
I use longer 3mm screw for the needle clamp. The stock is bit too short to secure the nut.
DIY a servo mount.
I use the ball link rod from my Trex450. You can use spare Trex600 servo link (the one connect the T-connector) , which is a perfect match/ length.
I change the ball inwards later, finding that the outer servo horn ball may touch the canopy.
Full lean position setup. Use the CarbSmart potentiometer to adjust. Actually, you can have servo travel by 80 degree only. I set :
Most Lean - 1 turn
"neutral/ failsafe" - 1 turn 4 click
Most Rich - 1 1/4 turn
Mount the sensor on os head. Use DIY aluminium sawdust mixed with A/B glue.
Since the sensor is easy to be destroyed on dismounting from the engine block , you can DIY your sensor by using a 100K thermistor, cost $2 only.
Must remember to adjust the gain after the initial setup as it is easy to leave the potentiometer at extreme anti-clockwise( during rich needle setup). This leaves the gain at zero. Now I adjust the gain to around 80%.
Installing carbsmart for almost 2 galloon, I finally can see my needle goes to richess position on landing. Actually Carbsmart save me today. My engine suddenly lost power after 4 mins. violent tic toc, piro-flip for 1 min, and funnel. The smokes get thicker and I land it immediately. I read the needle is at most counter-clockwise for almost 15 seconds!! I was surprised to find that the muffler back pressure hose was completely detached from the muffler !
What the hell! This cheap little gadget did save my engine! Last time my leaking hose blown my piston before I had this carbsmart!
More fine tune. The needle neutral position was turned more lean by few degree (see the circle). This make a huge difference and I can see the Carbsmart is now richen the needle at end of 3D. 3D flight is more powerful. Now the gain is set ~60%.
Sunday, November 25, 2007
Sunday, October 21, 2007
My first Nitro Heli- Trex600N Pro
Saturday, October 13, 2007
3S A123 Trex 450
Target at 3D.jpg)
.jpg)
@15T, 3000kv 450TH, HS 2300-2400 only.
3s A123 is 230g. However, the performance is far poorer than a 3s 2200mAH 18c lipo. Cos the voltage is low <9v>70 oC. For gentle flying, 3S A123 is perfect. Or you need a higher kv~3800 motor for 3S.
Another picture is a 3s lipo curve, @14T/ HS 2700-2800
Max power ~250W. Current <20a.
Tuesday, September 11, 2007
Tuesday, July 24, 2007
Hurricane Maintainence 300 flights

My flight logger of early setting with 7sA123, 600L 1600kv,14T, 61T/ 61T, 515mm carbon setting. Flight time 4.5 mins 3D. Voltage 20V, Amp 54A. My latest setting has power 1100W.
The swashplate has much free play at the central ball and the bearing. The central ball/hub freeplay is cured with thin CA (Do not do this if you are not sure). I am still thinking a non-destructive way to pull out the bearing.
The free play at the plastic tail grip (between bearings and the grip) is cured with some CA as filler. Actually, the stock tail set holds quite well even in funnel, fast backward and piro-flip.
Finally, I replace a Trex600 thrused tail grip and hub. What I need is a carbon tail blades to fit the stronger tail grip.
The copper tail slider hub needs replacement. The original copper slider has no thread. Since it still holds well in 3D, I do no change it.
The plastic main grip shows much freeplay and needs to put some CA at the outter bearing case to fill the gap before putting it back. The CNC rotor Hub shows some free play and needs some loctite. The dampener O-ring and spacer replaced.
Sunday, July 15, 2007
Learning Autorotation
I learn it like this...
1) DO NOT USE THROTTLE CUT/HOLD HIGH IN THE SKY AT THE VERY FIRST TIME. You cannot manage that. THe first thing is to FEEL how good the heli float at a certain headspeed. So start at 1 foot hovering above ground. Flip the throttle hold, and FEEL how it float. Then increase the height to 3,5,7, 10 foot , until you get some confidence and the pitch movement. Also make sure your pitch curve is consistent in hovering mode and throttle hold mode.
2) Then feel the drop down speed. In normal mode (with negative pitch set to -4 to -6), fly the heli high up, then lower the pitch/ throttle stick down steadily (but not killing the motor.) Make sure you DO NOT set the ESC to VERY SOFT START as the motor cannot spool up fast enough (for a rescue) in case a total shut down. Practise it and see how fast the heli drop and LISTEN to the rotor gaining head speed . Do not land the heli yet. Throttle up again at around 20 foot high. This is to train you FEEL of dropping velocity.
Repeat and decrease the throttle up altitude.
3) Finally, you can land your heli , still in normal mode. Bit by bit, lower the altitude. When you get confidence, you can practise flipping throttle hold when the heli is 1 foot above ground , then 3 foot, 5.....until you can flip it high in the sky.
N.B. remember flip the throttle hold switch BACK may cause the heli to piro like hell because the tail rotor speed is not high enough to counter the main blade rotor torque.
1) DO NOT USE THROTTLE CUT/HOLD HIGH IN THE SKY AT THE VERY FIRST TIME. You cannot manage that. THe first thing is to FEEL how good the heli float at a certain headspeed. So start at 1 foot hovering above ground. Flip the throttle hold, and FEEL how it float. Then increase the height to 3,5,7, 10 foot , until you get some confidence and the pitch movement. Also make sure your pitch curve is consistent in hovering mode and throttle hold mode.
2) Then feel the drop down speed. In normal mode (with negative pitch set to -4 to -6), fly the heli high up, then lower the pitch/ throttle stick down steadily (but not killing the motor.) Make sure you DO NOT set the ESC to VERY SOFT START as the motor cannot spool up fast enough (for a rescue) in case a total shut down. Practise it and see how fast the heli drop and LISTEN to the rotor gaining head speed . Do not land the heli yet. Throttle up again at around 20 foot high. This is to train you FEEL of dropping velocity.
Repeat and decrease the throttle up altitude.
3) Finally, you can land your heli , still in normal mode. Bit by bit, lower the altitude. When you get confidence, you can practise flipping throttle hold when the heli is 1 foot above ground , then 3 foot, 5.....until you can flip it high in the sky.
N.B. remember flip the throttle hold switch BACK may cause the heli to piro like hell because the tail rotor speed is not high enough to counter the main blade rotor torque.
Saturday, July 14, 2007
Hurricane EP550 New Frame
My old frame is >200 flights and is getting soft. Finally end its life on a crash from a low piro-flip. You can see the broken site and the surface area is less than 2mm x 8mm . This also contributes to the torsional weakness.
The new frame has new hex screws, better one way shaft bearing mount.
With 7s A123, the new fiber canopy fits perfectly without modification.
The new frame has new hex screws, better one way shaft bearing mount.
With 7s A123, the new fiber canopy fits perfectly without modification.
The new 61T is much harder and is not worn after 20+ flights.
Wednesday, July 04, 2007
Upgrade Align trex600 swashplate to 3mm
The old version is 2mm ball screw which is prone to fail /fracture.
With the new 3mm Align ball screws pack, you can make an upgrade to the old version swashplate.
First drill a 2.5mm hole to prime a very precise straight hole
, then use a 3mm thread cutter 絲攻.
Loctite the new 3mm ball screws.
The process takes 15 mins.
Monday, July 02, 2007
Eagletree Airspeed Sensor
Tuesday, June 12, 2007
Lama V3
T34 Mentor
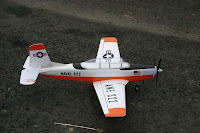

The first plane that I really can fly. Gear box with motor 300H. I flied this with my kids , and a trainer cord.
The plane is pretty stable depite its low wing config.
Unable to get spare parts and was converted to brushless motor and my first DIY motor mount.
Retired when uncontrollable roll depsite numerous repair.
The plane is pretty stable depite its low wing config.
Unable to get spare parts and was converted to brushless motor and my first DIY motor mount.
Retired when uncontrollable roll depsite numerous repair.
Subscribe to:
Posts (Atom)